Grinding and polishing rollers
In general, roller grinding and polishing are processes during which the desired part is smoothed and polished and ready to be used by special devices and according to specific principles.
If you have experience in the field of industry, you must know how annoying it is to work with tools and objects that have uneven and scarred surfaces. Stone and roller polishing are among the machining processes that are used to create a smooth and polished surface on metal parts. These processes are typically used to produce parts with high precision and excellent surface quality. We called this process roller polishing. Some others call this process polishing roller. Of course, both names are correct. You know that we need special tools to smooth and polish different surfaces. Today, in this article, we are going to discuss stone brushing and polishing of rollers and pieces. Follow us to the end.
History of roller grinding and polishing
At first, you may think that these two methods are modern. But it is not like this. Evidence shows that these techniques have existed since thousands of years ago. In ancient Egypt, these methods were used to produce weapons and agricultural tools. Over time, these techniques have improved and merged with today’s technologies. In the 19th century, with the development of machine tools, grinding became an industry. After some time, with the further development of technology, in the 20th century, the roller polishing method was inspired by grinding. In the beginning, these two methods were used to smooth and polish gears and different parts of machines. Today, these two methods have a great place in the world industry and are widely used.
What is grinding?
In general, grinding is a process in which a piece of metal is rubbed with a rotating emery stone to make its surface smooth and polished. Grinding stones are made of abrasive materials such as diamond, CBN or aluminum oxide. Grinding can be used to produce parts with high precision and excellent surface quality. This process can also be used to remove large amounts of material from the part. If we want to define this issue in another way, it should be said that grinding is the same process of removing extra materials from parts using abrasion. It is worth mentioning that this process usually takes place in the final stages of working on the part. After doing this, we can see a visible increase in the quality of the work surface. This process is also called leveling.
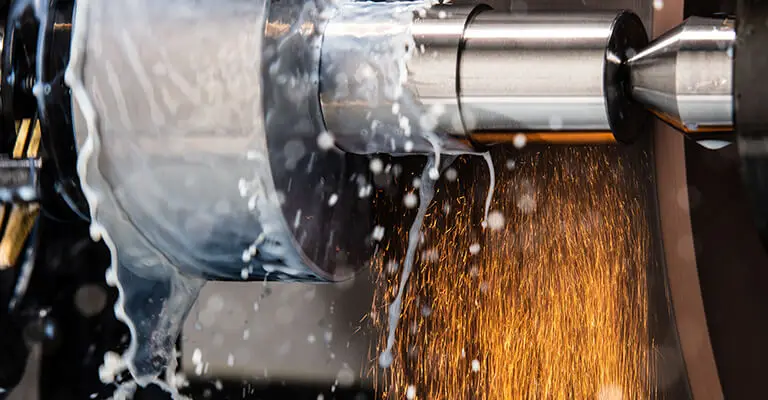
Types of grinding
There are different types of grinding. Naturally, each of these methods is used to perform a specific task. You should know which grinding method should be used in each situation, you should pay attention to the size, shape, properties and production rate of the product. Common types of grinding methods are:
flat grinding
In this type of grinding, the piece is placed on a fixed table and the sanding stone moves vertically. In this method, the piece is placed on the table by means of a clamp, which is called a clamp. The clamp is usually electromagnetic or works by using a vacuum. This grinding method is mostly done for steel and cast iron because these two elements are magnetic and can be easily held by a magnetic tool.
Cylindrical grinding
It is used for grinding surfaces and cylindrical objects and work combs. In this method, both the grinding wheel and the workpiece rotate at a certain speed. Then the abrasive surface is placed on the outer surface of the cylindrical part and grinding operation is done. It should be noted that by changing the shape of the abrasive head, it can be inserted into the inner part of the cylindrical body and grind the inner environment.
corner grinding
In this type of grinding, the piece is placed on a rotating table and the sanding stone moves vertically. This method is used when it is not possible to grind the corners of the parts. For this reason, the abrasive head part is designed a bit sharper and makes it possible to grind the corners of parts that are hard to reach.
Advantages of grinding
The first advantage of this method is to obtain a smooth and polished surface for all parts.
The second advantage of this method is the high accuracy of the final patches. This happens because it is done by precise and engineered machines. The result of this work is to clean the next work that is done using this part.
But another advantage of this method is that you can grind many hard parts. Filing using the grinding method is faster than doing the same thing using other methods.
The last advantage that we want to examine is the ability to cut and grind hot materials. By heat, we mean materials that have high heat. This issue may make the work a little difficult in other methods, but it does not cause a problem in the grinding method.

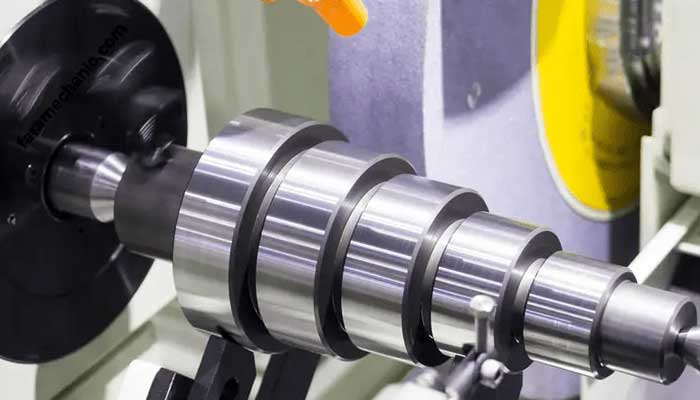
What is roller polishing?
Roller polishing or roller polishing is a process in which a piece of metal is rubbed between two rotating rollers to make its surface smooth and polished. The rollers are made of abrasive materials such as diamond, CBN or aluminum oxide. Roller polishing processing can be used to produce parts with high precision and excellent surface quality. This process can also be used to remove large amounts of material from the part. Using this method, you can easily polish steel and metal surfaces. The result of this work is having a completely smooth and suitable surface for the next activities. It is worth mentioning that this method can be done for other surfaces and other materials. But today, in the world of industry, most of the activists in the field of metal and steel use it.
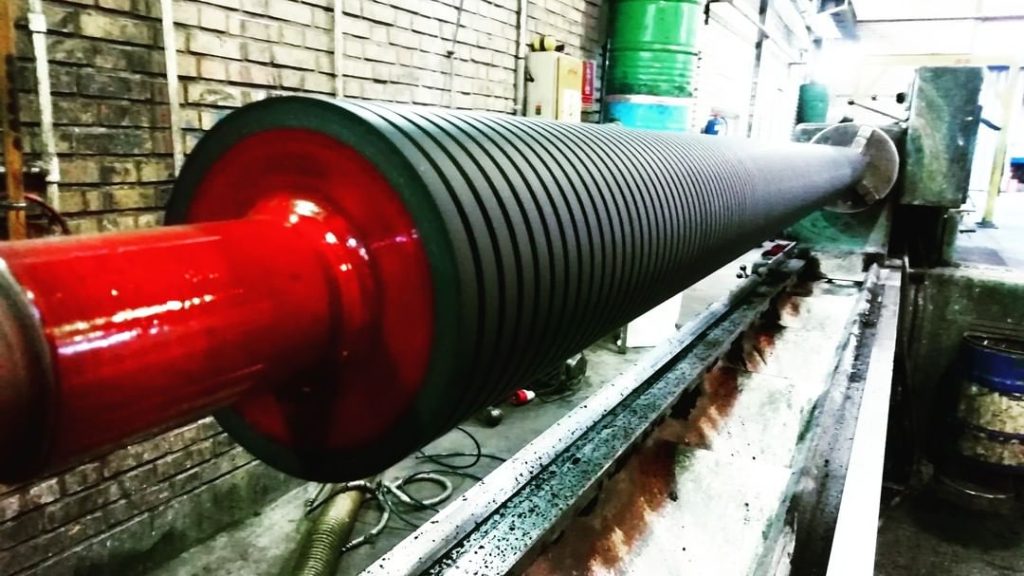
single phase
This method is the simplest type of roller polishing. The name of this method is single phase. what does it mean? It means that only one side of the roller is engaged in polishing. In this method, the piece is placed between two rollers. Then one of the rollers starts sanding one side of the piece. Simultaneously, the other side of the roller starts the polishing operation on the other part of the piece. Note that this polishing operation is done by Gilans.
Three-phase
But now let’s look at another method of polishing the roller. This method is a little more complicated and difficult than the previous one. It is also natural that it takes more time to do it. In this method, the power and electricity consumption is increased and both sides of the roller start the sanding process. After finishing sanding, it is time to polish the roller. At this stage, special wax is poured on the gilans and polishing and polishing operations begin.
Advantages of polishing rollers
But like grinding which had many advantages, roller polishing also has advantages. Of course, many of these benefits are similar, but it is not bad to take a look at them again.
The first advantage that roller polishing gives us is that in the end it gives us smooth and polished surfaces to use.
Another advantage is that it does not make noise when using it. It is also worth mentioning that compared to the grinding method, in the roller polishing method, there is more control over the sandpapers, which prevents them from being thrown out.
Another advantage of the roller polishing method is the better and easier control of the operator and the machine on metal and steel surfaces so that they do not come out of the machine.
But another advantage is that you can make parts in complex shapes.
Roller grinding and polishing applications
Roller grinding and polishing are used in a wide variety of industries. Having enough knowledge to use these methods, we can use them a lot. Some common applications of roller grinding and polishing are:
Automotive
You know that we need smooth and polished parts to make the interior and exterior of the car. Roller grinding and polishing is used to produce car parts such as wheels, engines and car bodies. In this way, the elements that we mentioned are easily prepared and together form an ideal car.
electronics
Roller grinding and polishing is used to produce electronic components such as transistors, capacitors and circuits. The production of parts with the right quality and level makes the tests more accurate and easier. What is the result? Achieving greater achievements.
Oil
Roller grinding and polishing is used to produce oil and gas parts such as pumps, valves and pipes. This issue is especially important in oil-rich countries such as the Middle East countries. They can expand their industries using this method.
Medical
Medical science is the most important knowledge in preserving human life. There is a high sensitivity for medical devices. The smallest mistake can lead to disaster. Roller grinding and polishing is used to produce medical parts such as implants, surgical instruments and medical equipment.
Comparison of grinding and polishing rollers
Grinding and roller polishing are both machining processes used to create a smooth, polished surface on metal parts. However, there are key differences between the two processes. With all that being said, ultimately choosing your preferred method depends on a number of factors. Among these factors, we can mention the type of part, the required accuracy and also the budget. The main differences between these two methods include the following.
In grinding, the sanding stone moves in a rotary motion and rotates the workpiece in a fixed path. In roller polishing, the piece is placed between two rotating rollers and the rollers grind the piece simultaneously. Actually, in the grinding method, human power is needed to control the stone, but not in the polishing of the roller.
Grinding is usually a faster process than roller polishing. Why do we say this? Because the dimensions of parts in grinding are smaller than the dimensions of parts in rough polishing. For this reason, the speed of the grinding process is faster than the speed of the roller polishing method.
Grinding is usually a hotter process than roller polishing. This is because in the roller polishing method, the power consumption of the motor increases automatically. Also, due to the electricity that reaches it more, the amount of heat decreases.
The future of roller grinding and polishing
You may be wondering if grinding and roller polishing will be used in the future? Our answer is definitely yes. Grinding and roller polishing are effective and efficient technologies that are widely used in various industries. We examined some of these industries, which are vital industries, in the previous parts. It is expected that these technologies will continue to grow in the future. Why do we say this? Because the world moves towards progress every day. Therefore, it is necessary to use these useful methods later in industries such as construction, decoration, etc.
Cost of grinding and polishing the roller
The cost of grinding and polishing the rollers depends on several factors.
The first factor is the type of roller. Metal rollers are usually more expensive than plastic rollers.
The second factor is the size of the roller. Larger rollers are usually more expensive than smaller ones.
The next factor is the amount of roller damage. If it is damaged a lot, the cost of grinding and polishing for it will be higher.
The next factor is the type of grinding. Coarse grinding is usually cheaper than fine grinding. Also, subbing is usually cheaper than polishing.
But if we want to have a comparison between their prices, the cost of polishing the roller is usually lower than the cost of grinding it. Of course, these are only as a general guide and may vary from region to region. Three types of sandpaper can be introduced as the best.
Correct choice of sandpaper
Sandpapers are all made with a common purpose. with the aim of smoothing and polishing different surfaces. Especially metals. Sandpapers have different qualities according to the construction material. Some of them may wear out quickly and with double use. But sometimes it is possible to use some sandpapers many times. In the following, we introduce some of the best sandpaper models to you:
It is one of the best types of sandpaper. In other words, it is a synthetic abrasive that has a long shelf life. It can also be used to smooth and polish the surface of metals and even hardwoods.
Another one of the best and most durable types of sandpaper. These sandpapers are very suitable for polishing metals such as steel, aluminum and bronze, and they are not easily destroyed.
We can confidently say that this type of sandpaper is the most durable and the best type of sandpaper. Synthetic silicon carbide abrasive can be used for sanding materials such as plastic, metal, hard wood, soft wood and even stone.
Thank you for your cooperation with us in this article. As you have seen, in this comprehensive article, we examined the grinding and polishing of rollers. We also told you a short history of them and examined their advantages and disadvantages. With the comparison made in this article, you can definitely decide which method is better to use for your activities. First of all, don’t forget that if you don’t have enough expertise in this field, be sure to consult an expert. We hope that the points mentioned in this article have been of interest to you and have been useful. Mabanapaya Industrial Group, having professional and specialized tools, is ready to start cooperation with you dear ones. You can contact our experts to find out about the conditions, prices and also get free advice.